Manufacturing execution and Advanced warehousing in Microsoft Dynamics 365/AX
Manufacturing execution functionality in Microsoft Dynamics 365 for Finance and Operations (D365FO) and Dynamics AX handles the registration of actual hours for Production order routing operations. Theoretically a production order can go through Start and Report as Finished (RAF) status by just using the registration functionality. With the arrival of Advanced warehousing in AX 2012 R3 the situation has become a little different.
Controlling the “Start” and “RAF” status for production orders via Time registration terminals requires the right parameter settings. In all cases, the Release will have to be done by the production office or supervisor.
Without release, a production order will not show up in the registration terminals (Job card Device or Job card Terminal).
Let’s see how the “Production order defaults (by site)” make it possible to manage the “Start” and “Report as Finished” status via the time registration terminal.
The parameters are found in Production order control/Setup/Manufacturing execution/Production order defaults (by site)
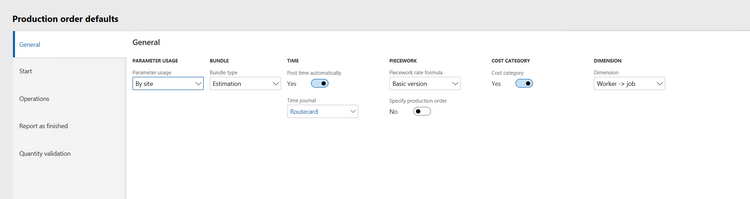
The parameters in this area control the behavior of production orders during the time registration process. They are valid for all users (in a site or in a company). The settings in “General” are not relevant for this blog.
Settings in the “Start” section
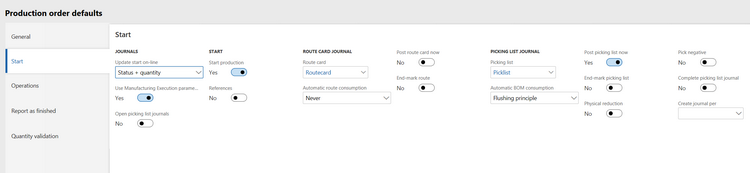
The biggest decision is the first parameter “Update start on- line”.
For real time production order status, it makes sense to have the value “Status + quantity”. The process will be straightforward. The production office (the supervisor) releases the production order. The first registration worker that starts working on operation 10 of this order automatically starts the production order with the quantity entered for operation 10.
This means that any Production BOM materials that have a flushing principle “Start” will now be backflushed.
With Advanced Warehousing, what is different with the automated “Start” process of a Production order in manufacturing execution?
The key difference with Advanced Warehousing is that we now are dealing with a “picked” status for each Prod-BOM item.
At release time or via a batch the system creates Warehouse work for “raw material picking”. This warehouse work will change the inventTrans status of each Prod-BOM line to “picked”. Without advanced warehousing the status ‘picked” was never used for Production order BOM materials.
After picking, the items still have to be “deducted”. Only using the flushing principle “Available on location” guarantees that the system only deducts the items/quantities that were picked. If we use the principle “Start” with advanced warehousing, we will run the risk of errors when not all items in the Prod-BOM were picked and we start the Production order with “Flushing principle” in the Bom-consumption field. “Available on location” is called this way because the Warehouse picking work has put the picked items in the put location which is the input location of the Resource group of operation 10, or to which operation the materials were linked. The items are “available in the input location of the Resource group”. The completion of the warehouse picking work moved them from their warehouse storage location to that put location that is the “input location” in the Resource group. They are now sitting there, ready to be backflushed.
General tab of the Resource group showing the Input location.
When using Advanced warehousing with Production orders, use the flushing principle “Available on location” on the BOM lines and make sure that the resource group in the routing operation has an input warehouse and an input location. With advanced warehousing, the flushing principle “available on location” is the only principle that is aware of the status “Picked” in the inventTrans table and will only flush (= deduct from inventory) what was picked. If we would use the principle “Finish”, we would have an issue just like we would have with “Start”. If not every item was picked yet, the system will not see that and will try to backflush all items with principle “Finish”. The principle “Available on location” will politely flush (= deduct) all inventory that had been picked and put the picked quantity into the input location of the Resource group.
NOTE
If we have to pick additional items later for the same production order (because some items arrived later), the system will almost instantly create and post a picking list after the warehouse picking work has been completed. (it takes a few minutes). This avoids having to manually post additional Picking lists for a production order. The parameter setting shown in the screen shot below will make this happen. It is the standard setting for backflushing, nothing special.
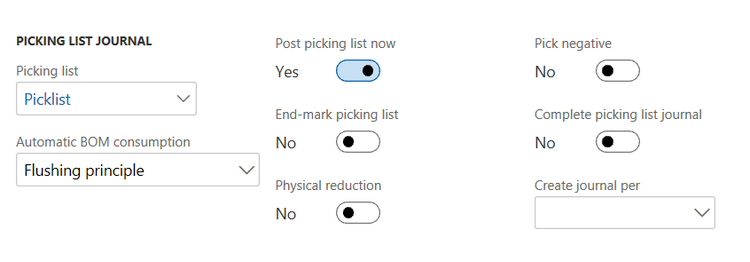
- Automatic BOM consumption: Flushing principle (which will be “Available on Location” which works like “Start” with the important difference that it will only flush what is in status “picked”.
- Post picking list now: This is obviously a Yes.
As always, we avoid the “End-mark picking list” and “Physical reduction”, “Pick negative”, and “Complete picking list journal” parameters like the plague (End-mark = yes would say that we will have no more picking for this Production order, “physical reduction” reduces the quantity on the Prod BOM to whatever we happen to have on-hand, Pick negative would only work if we allow negative physical inventory in the Item Model group, which we typically do not and “Complete” is creating a picking Journal for all lines in the Prod-BOM regardless their pick status or their on hand availability which would disrupt our process).
Now we will discuss the next fast tab in the Production order defaults (per site), “Operations”.
Settings in the “Operations” section
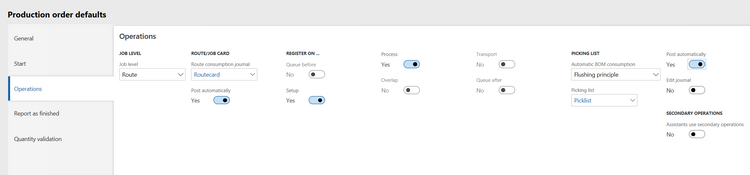
FREE Membership Required to View Full Content:
Joining MSDynamicsWorld.com gives you free, unlimited access to news, analysis, white papers, case studies, product brochures, and more. You can also receive periodic email newsletters with the latest relevant articles and content updates.
Learn more about us here