The Past, Present and Future of Asset Management and Enterprise Resource Planning Integration in Manufacturing
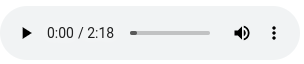
FREE Membership Required to View Full Content:
Joining MSDynamicsWorld.com gives you free, unlimited access to news, analysis, white papers, case studies, product brochures, and more. You can also receive periodic email newsletters with the latest relevant articles and content updates.
Learn more about us here
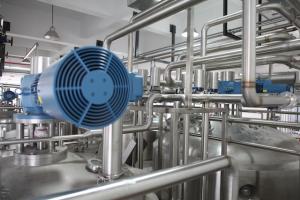
In the dynamic and highly competitive manufacturing landscape, effective asset management stands as the cornerstone of success. Manufacturing plants rely heavily on various assets such as machinery, equipment and tools, and improved asset management yields improved productivity, utilization, and equipment longevity. There has been a marked evolution in how manufacturers leverage asset management in their operations, with greater focus on improving the connection between asset management platforms and enterprise resource planning systems (ERP). In this article, I will talk about the past, present and future of asset management and ERP, particularly for Microsoft Dynamics 365 Finance and Supply Chain Management and Dynamics AX users in the manufacturing industry, and how methods have evolved in maturity and value.
The Past
During my 25 years of experience consulting in manufacturing and distribution, I have noticed that when it comes to asset management, most companies use either a stand-alone, home-grown solution or asset management software that has been interfaced to a back-end ERP. In many cases, paperwork, such as work order requests, work orders, repair specifications and spare parts lists, still underlies this somewhat antiquated approach. The asset management software would at least track work orders, but could be managing maintenance, repairs, and operations (MRO), inventory, purchasing, technician scheduling, and supply and demand planning or, more often, some subset of those areas. Even in cases when the ERP offered asset management support, the purchasing, inventory management and scheduling functionality were still in a different code base from the equivalent capabilities for operations and had distinct training and usage.
The trend toward running a stand-alone, home-grown asset management solution dominated the manufacturing industry in past decades. But as most companies now understand, a system that is separate from or at best interfaced with your ERP system is a sure-fire way to create siloes in your processes and data. There are several drawbacks to this method, including:
- Limited functionality: Home-grown solutions often lack the further enhancement and robust features and capabilities found in dedicated commercial asset management software. This limitation can hinder your ability to effectively manage assets, track their performance, and make data-driven decisions.
- Scalability challenges: As your organization grows in this increasingly competitive world, your asset management needs are likely to expand as well. Home-grown solutions may struggle to keep up. Modern platforms that improve software communication with equipment, such as services running in Azure or AWS, may be out of reach.
- Data security risks: Home-grown and older stand-alone solutions may not have the same level of security as integrated ERP software, such as Microsoft Dynamics 365 Finance and Supply Chain Management. Inadequate security measures can expose your asset data to breaches, potentially compromising sensitive information and putting your organization at risk.
- Lack of integration: Stand-alone solutions may not easily integrate with other business systems, such as ERP or maintenance management software. This can result in data silos, manual data entry and reduced operational efficiency. Asset management functionality that is separate from the ERP system means one more software vendor and one more issue escalation process.
- Dependency on in-house expertise: Maintaining a custom asset management solution relies heavily on the expertise of in-house developers. If key personnel leave or expertise is lacking, it can lead to difficulties in supporting and enhancing the system.
The Present
In today’s manufacturing environment, there has been a clear shift from having siloed, home-grown asset management solutions to having asset management functionality imbedded into ERP systems. One very successful example of this is with Dynamics 365 Finance and SCM, which has asset management functionality written directly into Microsoft Dynamics as standard features. The integration includes the exact same purchasing, inventory management, advanced warehouse management (mobile), MRP and project accounting that operations was already using and adds:
- Maintenance work orders either for ad hoc repair or as part of well-defined preventive maintenance standards
- Standard repair work templates for materials, staff and equipment usage
- Preventive maintenance templates that included triggers such as elapsed time, machine run time, mileage or any other trackable variable
- Manufacturer specs including recommended spare parts.
Using this method, all cost and financial data is captured by project accounting, and every work order is a child project to a parent project, which might be a machine or even equipment retrofitted to the machine. This allows the entire cost history of maintaining a piece of equipment to be easily exposed for analysis and general accounting. Combined with fixed asset depreciation logic, a full cost of ownership can be illuminated.
While Microsoft was not the first and is not the only ERP vendor to offer integrated asset management services, it is one of the most seamlessly designed with its functionality written directly inside of Dynamics 365. The benefits of leveraging an ERP that has built-in asset management functionality are plenty:
FREE Membership Required to View Full Content:
Joining MSDynamicsWorld.com gives you free, unlimited access to news, analysis, white papers, case studies, product brochures, and more. You can also receive periodic email newsletters with the latest relevant articles and content updates.
Learn more about us here