How well does Dynamics 365 Business Central fit a GP manufacturing user’s needs? Quantify it.
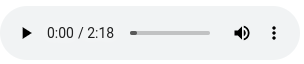
FREE Membership Required to View Full Content:
Joining MSDynamicsWorld.com gives you free, unlimited access to news, analysis, white papers, case studies, product brochures, and more. You can also receive periodic email newsletters with the latest relevant articles and content updates.
Learn more about us here

Many manufacturing companies that use Microsoft Dynamics GP are considering upgrading to Dynamics 365 Business Central (BC). However, this decision is not as simple as it may seem. Here are some reasons why:
- GP was not designed for manufacturing. GP was initially a financial and accounting solution, and third-party vendors added its inventory and manufacturing modules later. This means that GP may not have met the specific needs of many manufacturers, and they may have had to compromise or customize their systems.
- GP partners may not have manufacturing expertise. The Dynamics GP partner network is well-known and respected but may not have a strong focus or experience in selecting and implementing manufacturing ERP solutions. This could affect their ability to advise and support GP manufacturers who want to migrate to BC.
- BC may not be the best fit for all manufacturers. BC is a modern and cloud-based ERP solution that offers many benefits, but it may not suit every type of manufacturing. For example, BC may not have the functionality or flexibility to handle complex or multi-mode manufacturing scenarios, such as engineer-to-order, make-to-order, or mixed-mode.
With those facts as a backdrop, here are some recent examples of why a comprehensive assessment is even more critical for Dynamics GP manufacturing companies contemplating a move to BC:
- Summit North America Circle of Excellence Feedback: I was the lead HandsFree consultant in the ERP Circle of Excellence (COE) Lounge at Summit NA. The COE was set up to offer ERP project advice to anyone with questions regarding their project, regardless of its stage or status. In that setting, I was approached by several former GP manufacturing companies regretting their selection of BC. In each case, I was able to diagnose the issue with one straightforward question: what type of manufacturing does your company do? For example: Assemble to Order, Process, or Engineer to Order (ETO).
- User Group Poll: I reviewed a recent poll conducted by a Dynamics User Group that asked GP companies what direction they were planning for their post-GP ERP solution. Two results stood out to me:
1) The majority responded with “I don’t know” and “a non-Microsoft” answer.
2) Exactly zero responded with Dynamic 365 F&SCM as their option.
These are equally depressing and alarming results because they show that GP manufacturing companies don’t realize the great Microsoft manufacturing ERP options available to them or have had such a negative experience that they don’t know where to go or want a non-Microsoft solution. - Comprehensive Discovery Assessment: There is an engineering concept for looking at problems without an exact solution (investigating phenomena at the extrema). An ERP software selection is a problem without a clear answer. However, I gained many insights by investigating the fit of BC for an enterprise, multi-mode manufacturing company. That corresponding fit-gap analysis of critical functional capabilities was approximately 52 percent for BC and 88 percent for F&SCM.
GP manufacturers should take advantage of the Microsoft-sponsored discovery projects to avoid these pitfalls. This free and comprehensive assessment tool helps you evaluate your current and future ERP needs, compare different Microsoft Dynamics solutions, and identify the best fit for your manufacturing business.
Our team trusts the GYDE365 Discover Survey because a structured assessment tool helps GP users assess their current state and the feasibility of next steps. Such a tool identifies critical elements in their planning such as:
- What type of manufacturing do you do? Different manufacturing modes have additional ERP requirements. For example, discrete manufacturers need to manage bills of materials, routings, and work orders, while process manufacturers need to handle formulas, recipes, and batches.
- What are your critical functional capabilities? Every manufacturing business has its unique processes and challenges. You need an ERP solution that can support your core operations and enable you to improve your efficiency, quality, and profitability. Providing a trusted fit-gap analysis requires an assessment of all relevant capabilities of the ERPs you are considering.
- What are your ERP project goals and expectations? Moving to a new ERP solution is a significant undertaking that requires careful planning and execution. You need to have a clear vision of what you want to achieve and how you will measure your success. A structured assessment helps your executives set your ERP project goals and expectations and align them with the best ERP solution.
Don’t make the mistake of choosing the wrong ERP solution for your manufacturing business. Take the time to assess, analyze, and evaluate which Dynamics 365 solution is right for your organization’s future.
...
Photo by Minku Kang on Unsplash
FREE Membership Required to View Full Content:
Joining MSDynamicsWorld.com gives you free, unlimited access to news, analysis, white papers, case studies, product brochures, and more. You can also receive periodic email newsletters with the latest relevant articles and content updates.
Learn more about us here