Getting Started with Production Floor Execution in Microsoft Dynamics 365 Supply Chain Management
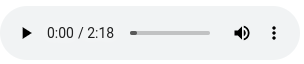
FREE Membership Required to View Full Content:
Joining MSDynamicsWorld.com gives you free, unlimited access to news, analysis, white papers, case studies, product brochures, and more. You can also receive periodic email newsletters with the latest relevant articles and content updates.
Learn more about us here
This article was co-authored by Amol Thakare, principal consultant at Wipro.
With industry 4.0, customers require Manufacturing Execution System (MES) capabilities embedded with their ERP solutions. Microsoft Dynamics 365 Supply Chain Management offers some MES features with a specific interface optimized for shop floor technicians without requiring a user specific license.
Production Floor Execution in Dynamics 365 Supply Chain Management (SCM) is designed to help manufacturers manage and streamline their shop floor operations. It is intended to be used by any employee who has time and attendance tasks to execute or production operations to perform.
In this article we will examine how manufacturers set up devices with Production Floor Execution and configure them to improve the efficiency and data collection duties of employees as they perform their jobs. We also provide some ideas for how to build on the fundamentals to introduce more advanced scenarios.
Pre-requisites
To use Production Floor Execution, your organization must be running D365 SCM version 10.0.40 or later. Other pre-requisites include:
- Register material consumption on the production floor execution interface (non-WMS) (As of Supply Chain Management version 10.0.32, this feature is turned on by default.)
- (Preview) Register material consumption on the production floor execution interface (WMS-enabled)
- Tracked components is a feature that lets workers and managers register batch/serial numbers for materials and components that are used in manufacturing processes. You must make the feature available to workers by adding a Tracked components button to the appropriate tab and toolbar, as described in Design the production floor execution interface.
Key Components
Here are the Manufacturing execution menu items in the Production control module. The two areas serve different purposes. Using the list on the left, users can do transactions and accomplish daily activities. The menu items on the right are meant for configurations and only managers or administrators will have access to them.
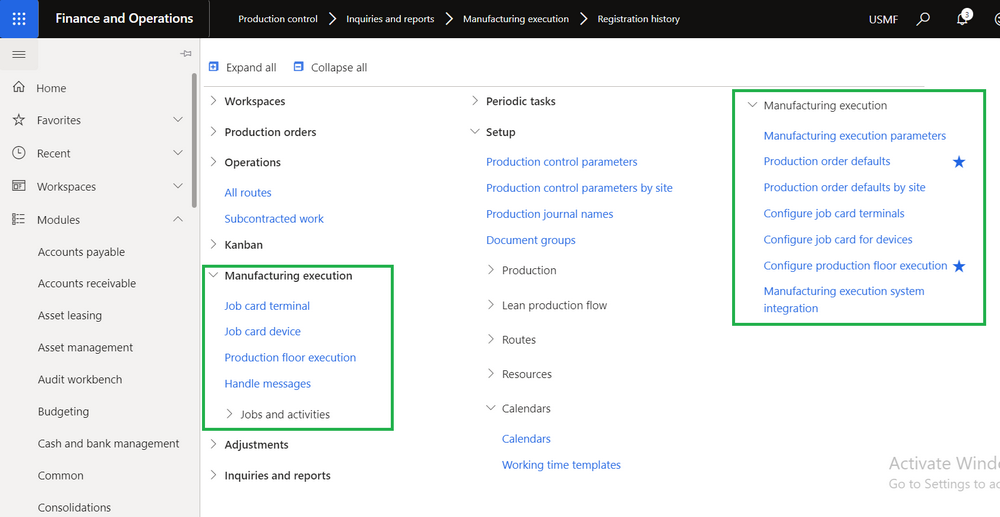
Parameters setup
In this section we will look at the various sections of production order settings and the parameters that an organization should define. This is configuration setup done by production managers and administrators.
As shown below, there are five key sections to the parameter setup:
- General - General parameter settings for production jobs in Manufacturing execution.
- Start - Parameters that are used when production operations are started.
- Operations - Parameters that are applied to production operations and feedback about operations during the production process.
- Report as finished - Parameters that are used when items are reported as finished on the last operation of a production order.
- Quantity validation - Parameters that are used to validate startup and feedback quantities on production orders.
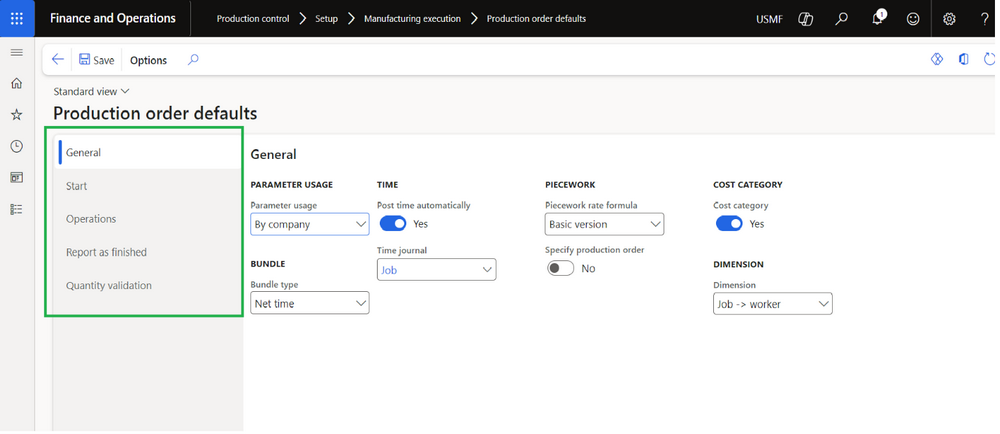
Types of production jobs
On the Operations tab, select which types of production jobs require registration.
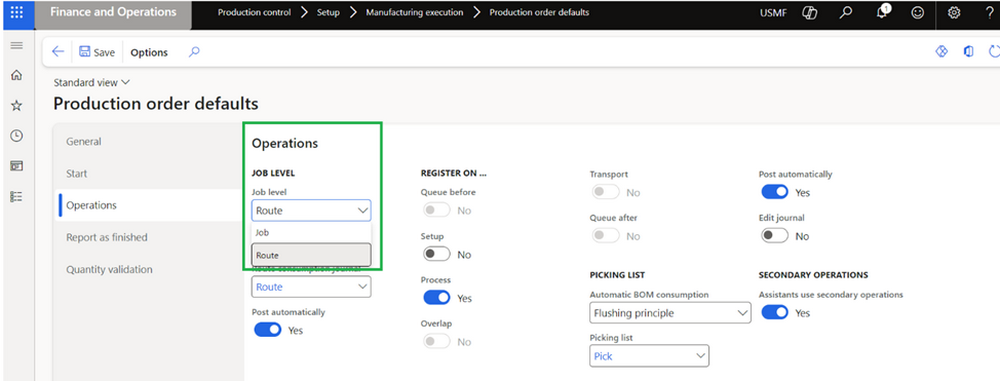
Typically, workers make registrations on setup jobs and process jobs. However, if job scheduling is applied, user can select other job types that workers must make registrations on when production orders are processed. Make sure to select all relevant job types. Otherwise, jobs might not be available for registration.
In the Route Groups setup, shown below, use the following parameters for each one:
- Activation: Select this option to enable calculations and scheduling for the selected job type, and to receive feedback
- Job Management: Select this option to include the job type in job management when running job scheduling.
- Working time: Select this option to schedule the job type according to the working time calendar defined for the operations resource.
- Capacity: Select this option to reserve capacity for the job type when running job scheduling. If this option is selected, capacity is reserved when scheduling is run for the selected job type. This gives you an overview of which job types in each route group use the operations resources.
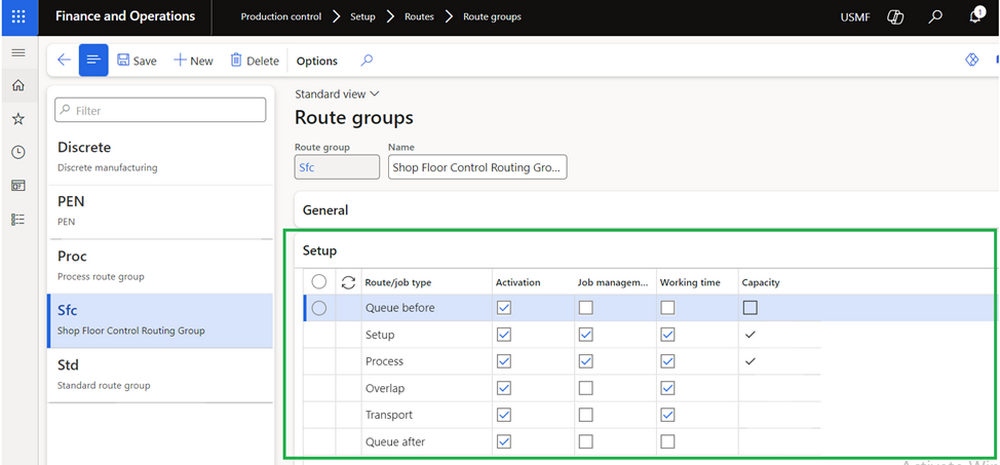
Route group is set up per operation. When a production operation is created, information from the route group is transferred to this operation.
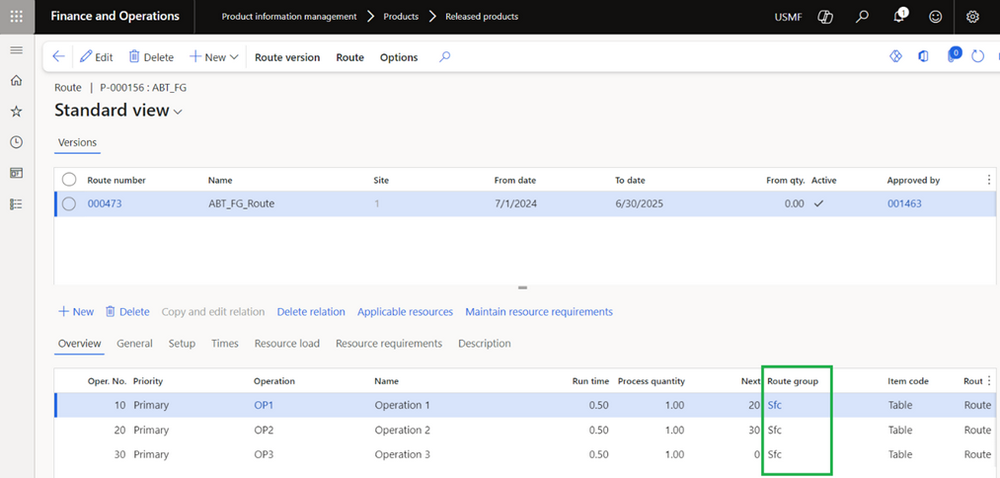
Configure production floor execution
For the Configurations please refer to Configure the production floor execution interface - Supply Chain Management | Dynamics 365 | Microsoft Learn
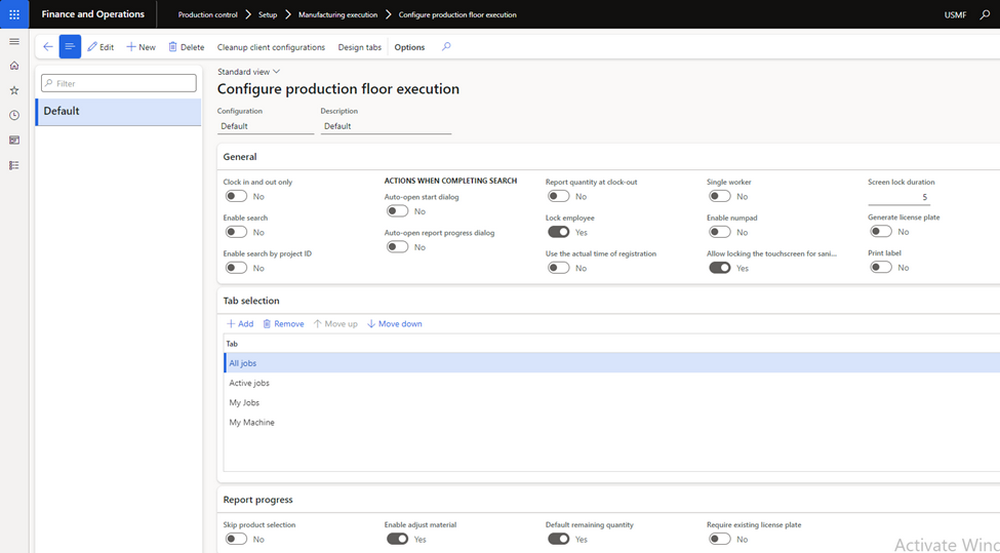
Time registration workers
Time registration workers can enter different types of time registrations, for example, clock in, clock out, register indirect activities, and absence registration.
If Time and attendance used together with Manufacturing execution, all registrations on projects, project activities, indirect activities, absence codes, and overtime and flex time will be recorded and are used to calculate payroll.
FREE Membership Required to View Full Content:
Joining MSDynamicsWorld.com gives you free, unlimited access to news, analysis, white papers, case studies, product brochures, and more. You can also receive periodic email newsletters with the latest relevant articles and content updates.
Learn more about us here